
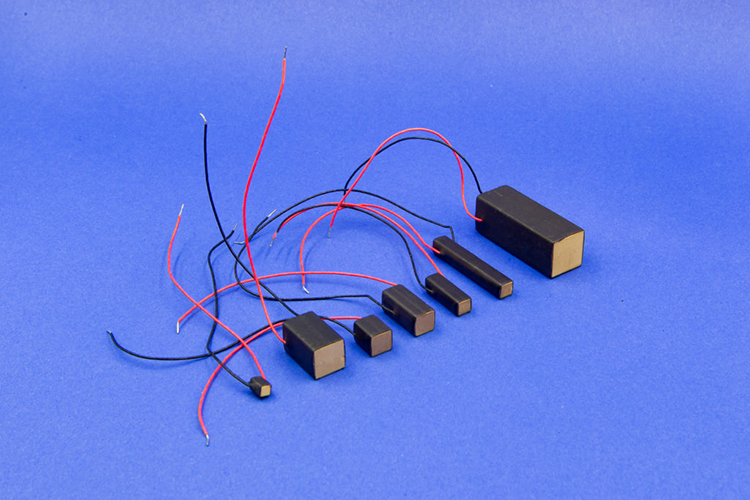

Due to producing a significantly higher current with no electromagnetic interference, such piezo generators are excellent solid state batteries for electronic circuits. By utilizing a different configuration of piezoelectric ceramics, techniques used to make multilayer capacitors have been used to construct multilayer piezoelectric generators.
#PIEZO ACTUATOR AND SENSOR GENERATOR#
The resulting electrical energy of a single-layer generator generates a high voltage at a low current over an incredibly quick timeframe. The force of the hammer exerts itself on a single-layer, rod-shaped piezoelectric ceramic, thus producing voltage and causing the necessary spark gap that ignites the fuel source. In these piezoelectric applications, the ignition button attaches to a spring-loaded hammer.
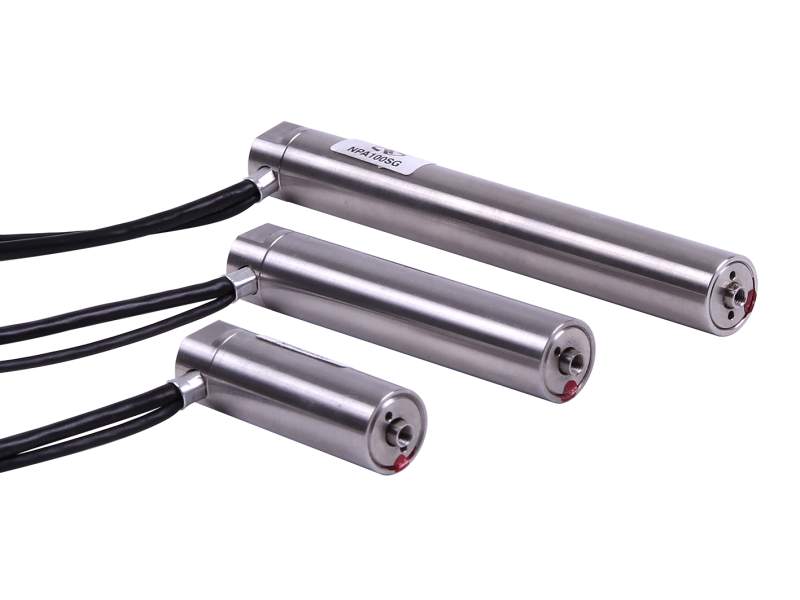
Piezoceramic ceramic devices fit into four general categories: piezo generators, sensors, piezo actuators, and transducers. For any particular application, however, limiting factors include the size, weight, and cost of the piezoelectric system. Finally we present some experimental results obtained on the scaled (1/7) rotor.A piezoelectric system can be constructed for virtually any application for which any other type of electromechanical transducer can be used. And all installed shunted passive PZT patches will damp high vibration frequencies, simultaneously rising stability of the control loop. We propose an approach according to which all active controlled PZT patches are driven at narrow frequency band filtering preferentially on a first eigenfrequencies. On other hand, at active control the stability of control loop can be lost at some vibrations and feedback parameters. On basis of numerical simulation it is shown that passive damping mode is efficient in the high frequency range only. We also perform a comparative investigation of active and passive (shunted by electric circuit) PZT actuators working modes. In the presented study we try to find the optimum type (bimorph or unimorph), places, and sizes of plate-like actuators and sensors attached to a composite spar undergoes the bend and twist load. The purpose of our investigation was decreasing a number of control channels at saving good vibration damping efficiency. One of the greatest technical difficulties of rotor blade active vibration damping is the necessity to transmit to a blade the number of high-voltage command signals through the rotated hub.

On the basis of this analysis we deduce the principal requirements to smart vibration control of rotor blades.
#PIEZO ACTUATOR AND SENSOR FULL#
First we consider a problem of vibration reduction in the helicopter rotor blades, more particularly, the features of rotor blade dynamics and approach to ensuring a dynamic similarity between full scale and scaled rotor blade. In the presented chapter some theoretical and real-world approaches to design and implementation of aircraft structures smart vibration control on the basis of controlled by feedback and shunted by external circuits power PZT patches are presented.
